3Dプリンター (Original Prusa i3 MK3S Kit) を買って組み立てた
3Dプリンターキット (Original Prusa i3 MK3S Kit) を買った。少しずつ組み立てて、サンプルデータを印刷するところまでたどり着いた。組み立ては、毎日1〜2時間づつ進めて約8時間かかった。
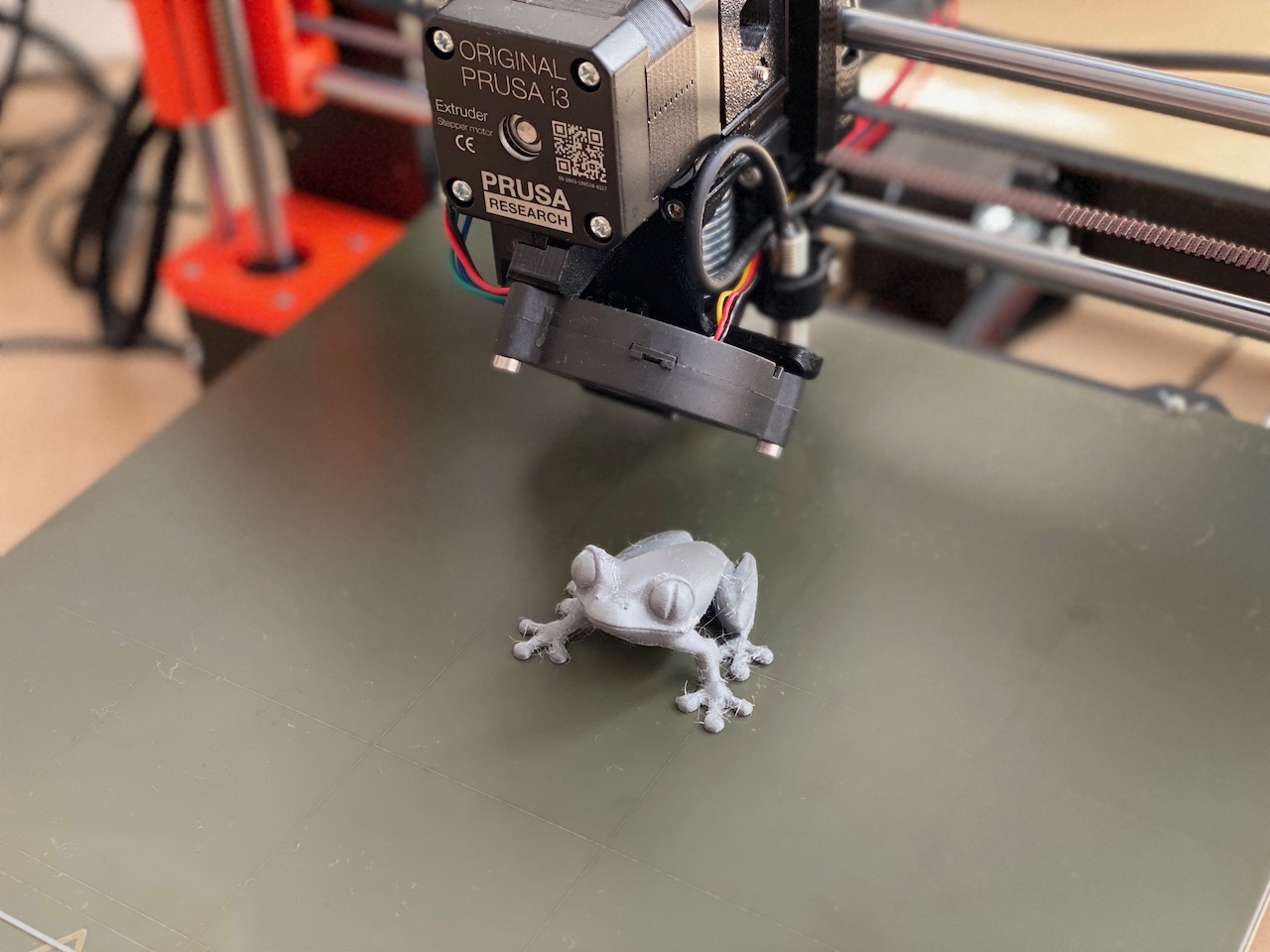
Original Prusa i3
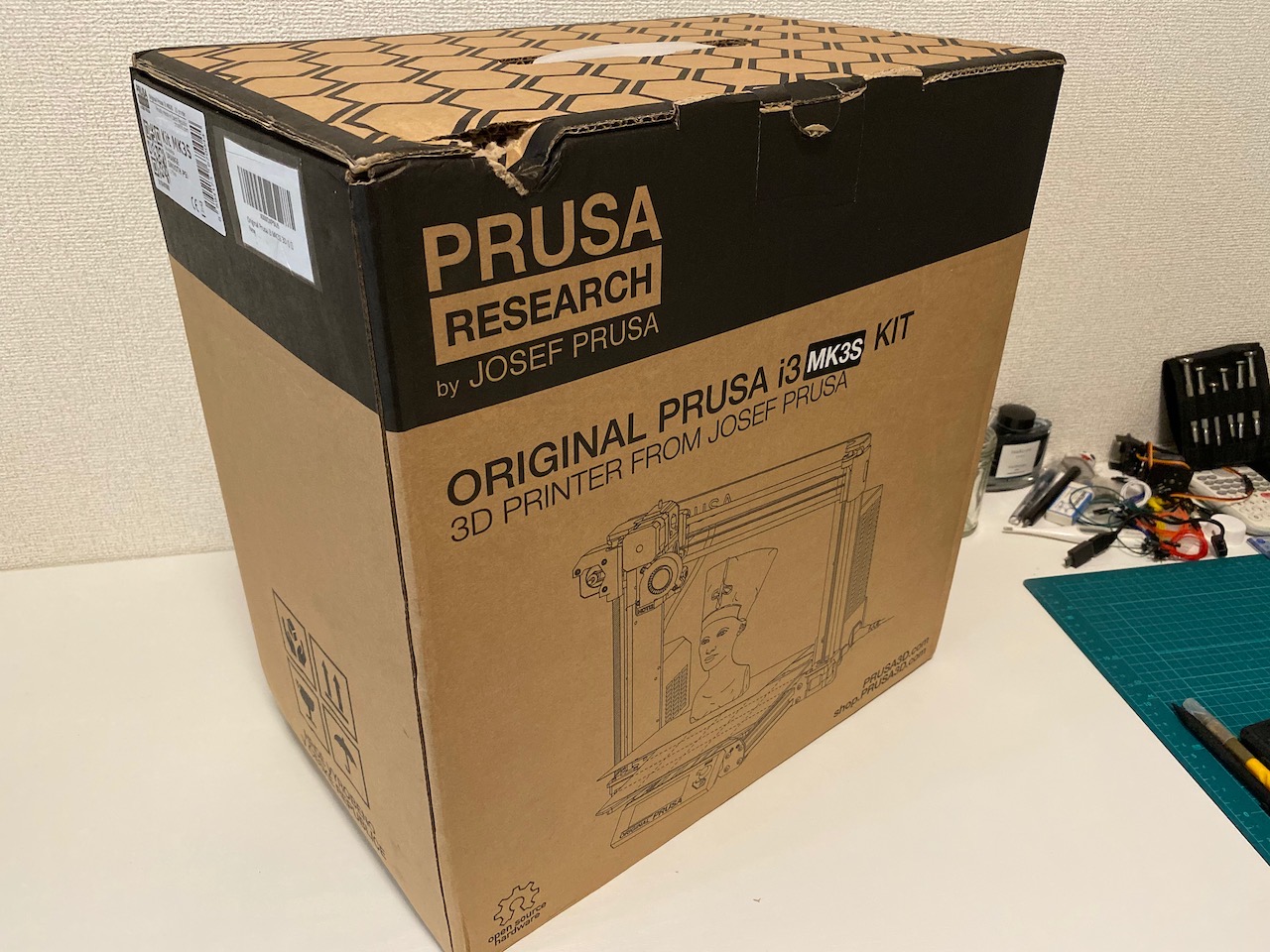
価格と性能のバランスがいいという評判で、Makeとかでもおすすめされている。YouTubeで海外の3Dプリンタ系のチャンネルをみるとよく出てくる。世界的には良く売れている機種で、既に10万台以上売ったようだが日本での知名度は高くない。最新版はMK3Sというモデルだ。
“Prusa”という名称は開発者の Josef Prusa から。てっきりアメリカ人か何かだと思っていたら、チェコ人のお兄さんだった。髭面のオヤジに見えるが、1990年生まれで、まだ20代。
オーンソースハードウェアなので、これを派生させたプリンタがいろいろと存在する。Amazon.co.jpで上位にいる中国メーカーのものは実はそれが多かったりする。
面白いと思ったのは、このプリンタのパーツも3Dプリントで製造されている点だ。
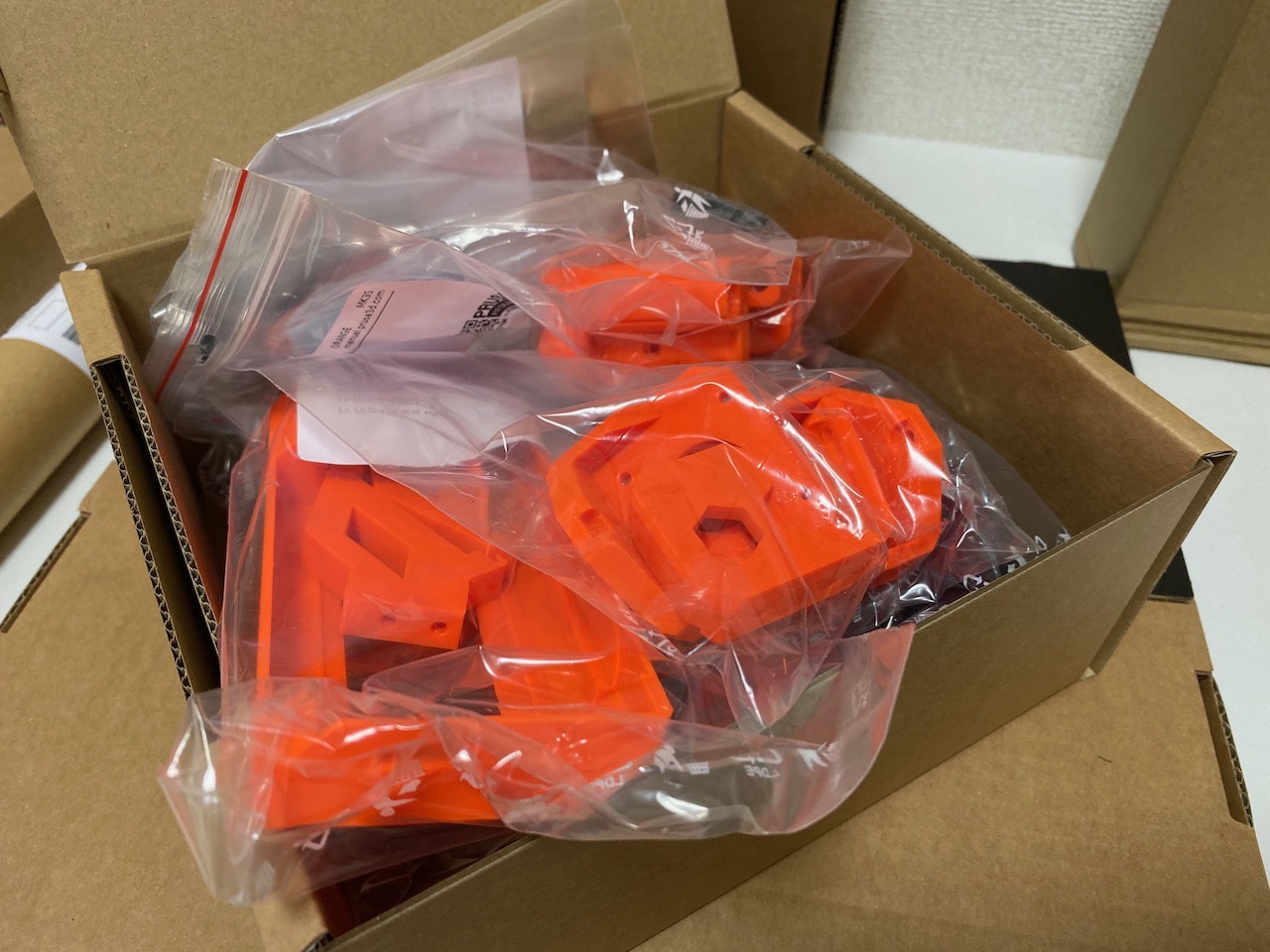
自分で組み立てるKit版と、組み立て済み版がある。組み立て済み版は値段が1.5倍くらいする。
購入は、チェコ本国のサイトとAmazon.co.jpでできるが、送料と消費税を考えると両者の価格に大きな差はない。自分はAmazonでKit版を買った。
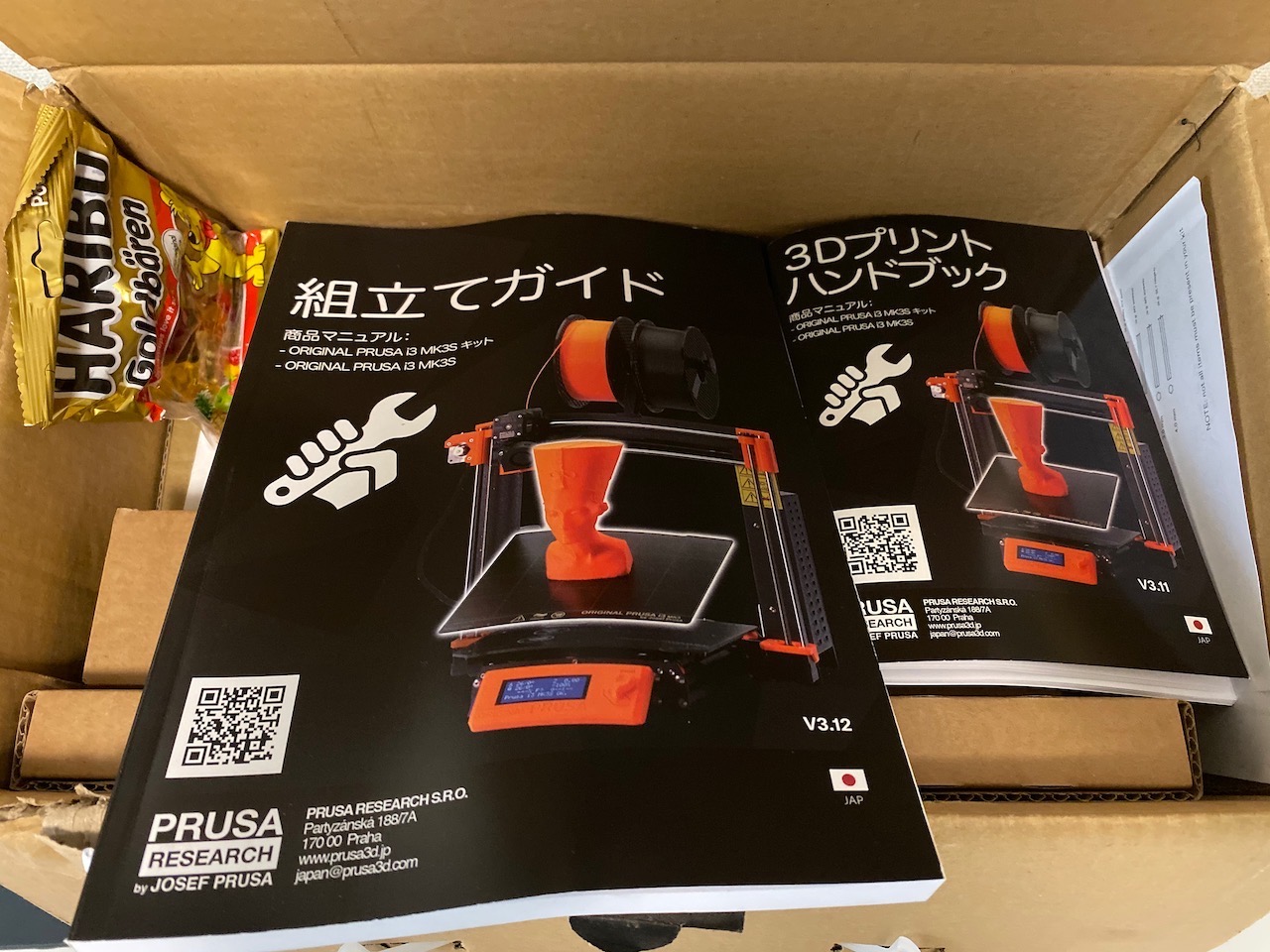
ダンボールを開けたらHARIBOが入っていて笑った。組み立てマニュアルの各章のおわりに「ここでHARIBOを5個食べましょう」とか書いてある。
Amazon.co.jpで買うと日本語マニュアルが付いてくるけど、公式サイトには最新の英語版マニュアルがあるので、英語がすごく苦手でなければ特に要らないかも。
組み立てる
自分は組み立てに8時間掛かった。作業に専門的なスキルは要らなかったしマニュアルも十分にわかりやすかったし専門的な工具も要らない。でも、組み立ては楽とは言えないし精神的にもけっこう疲れた。とはいえ一度組み立てると構造が分かるので、その後のメンテナンスのことを考えると一度は自分で組み立てたほうがいいと思う。
外箱を開封すると小箱が出てくる。
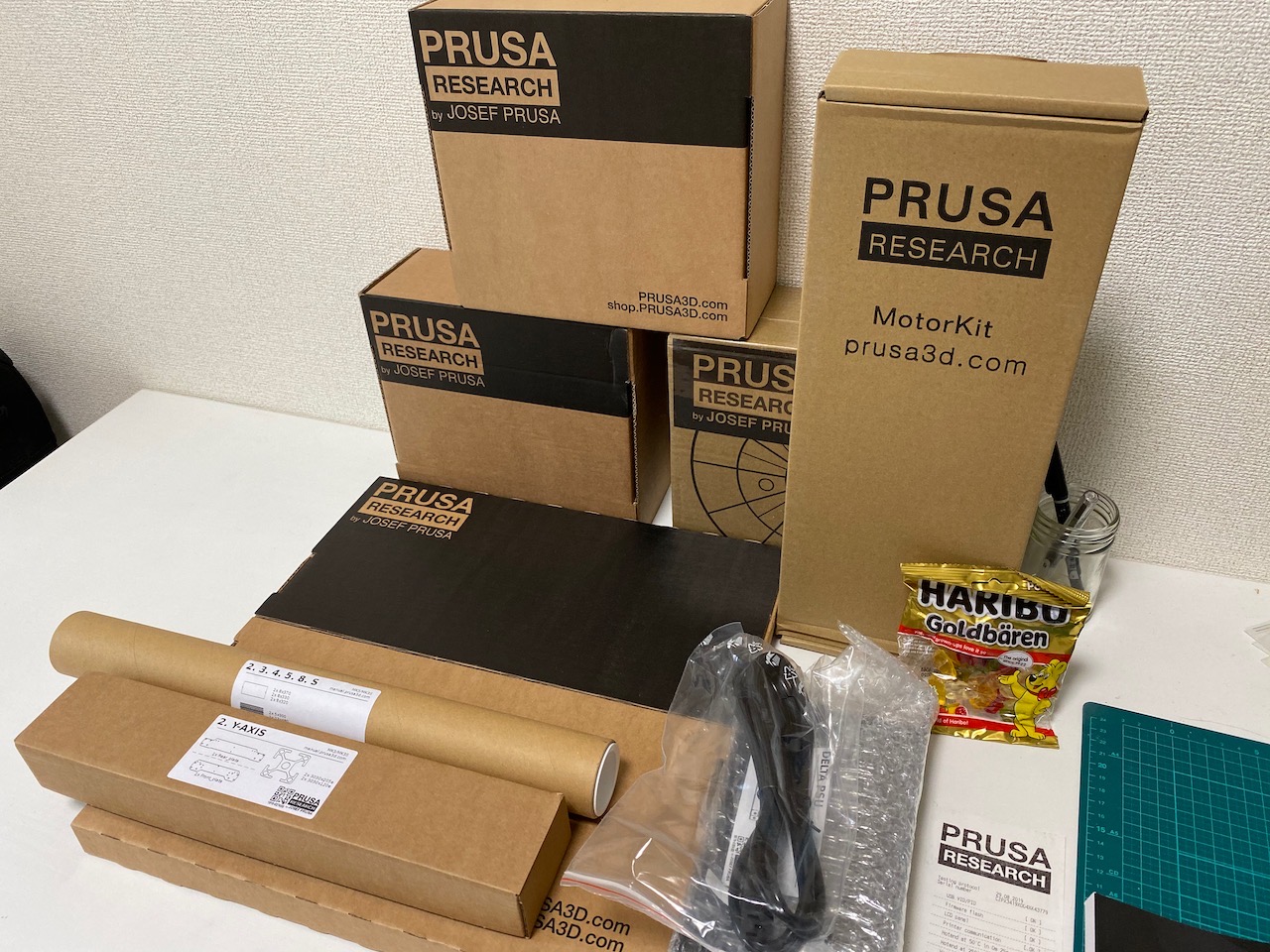
小箱を開封すると、パーツが現れる。
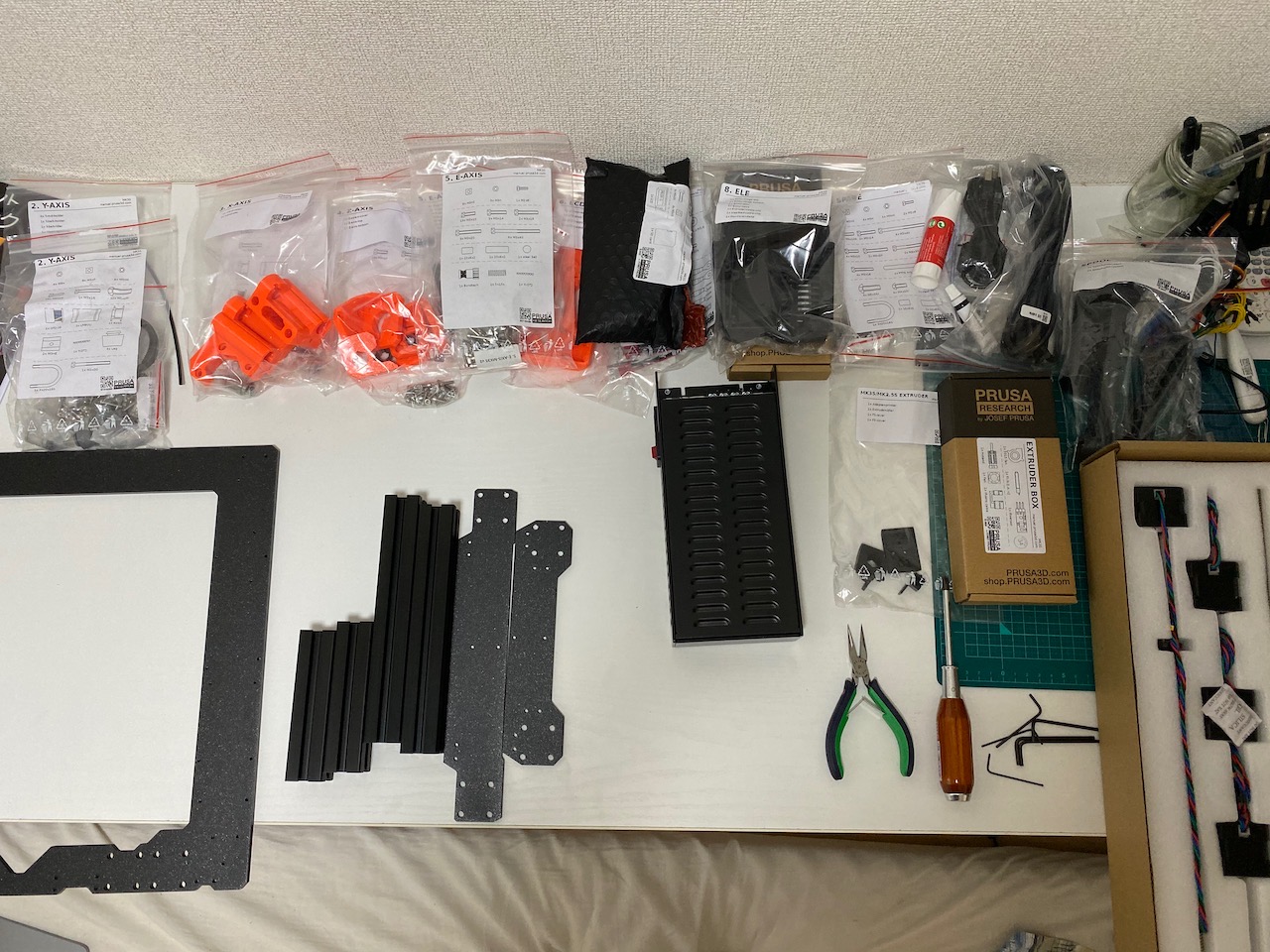
まずは骨格を組み立てて、そこにY軸(奥行方向の軸)を作る。骨格はさすがに剛性と精度が必要なので、3Dプリントではなく、金属を切削加工したものと、アルミの押し出しで作られている。
このへんの組み立ては簡単。
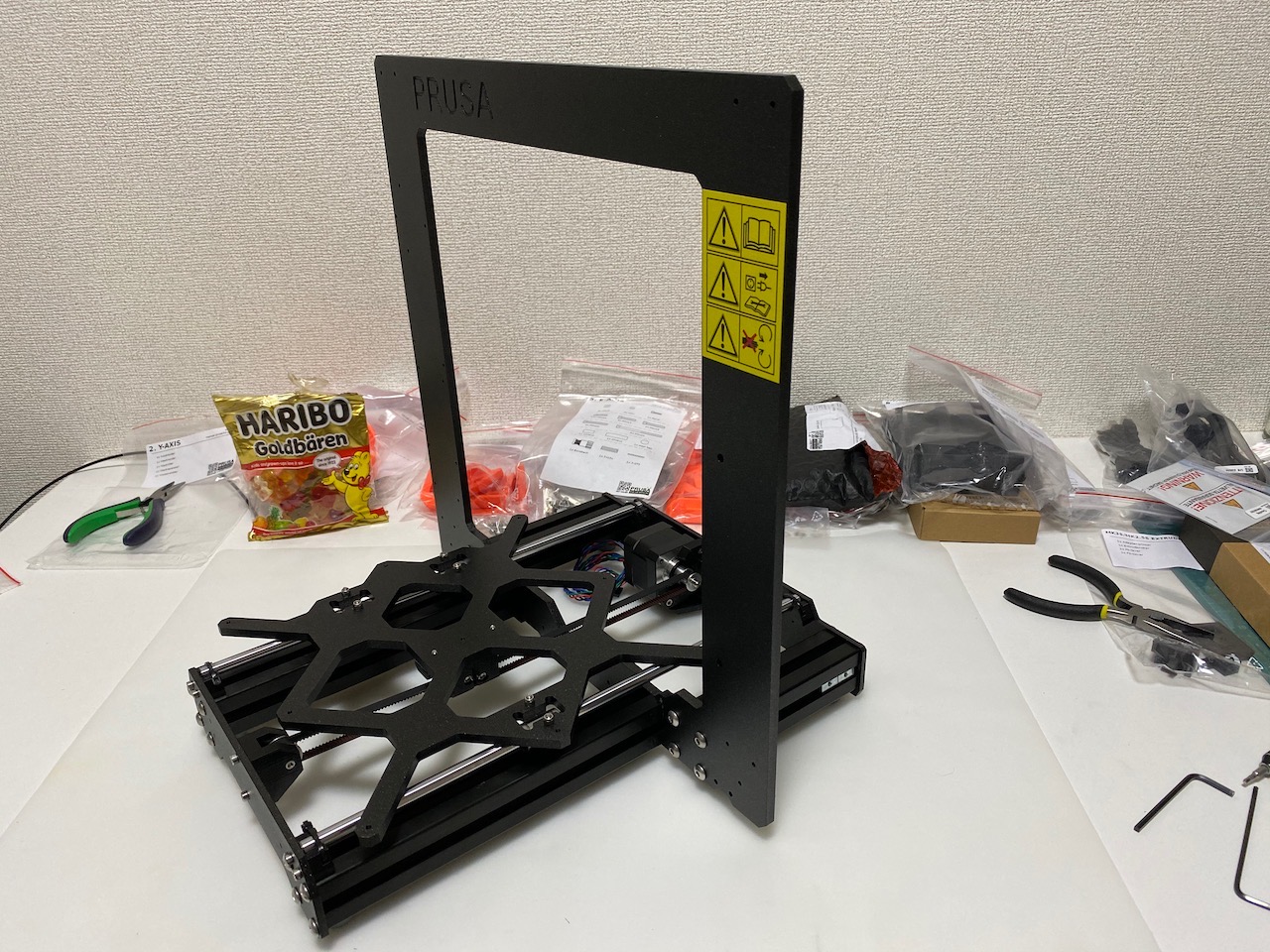
次は、Z軸(高さ方向の軸)とX軸(横方向の軸)を組み立る。(写真撮り忘れた)
その次にエクストルーダーを組み立てる。これはインクジェットプリンタでいう「ヘッド」に相当する部分。マニュアルにも書いてある通り、これの組み立てが最難関。このエクストルーダも、電子的なパーツ以外はすべて3Dプリント部品でできている。(このへんも写真撮り忘れた)
組み上げたエクストルーダを、X軸に取り付ける。
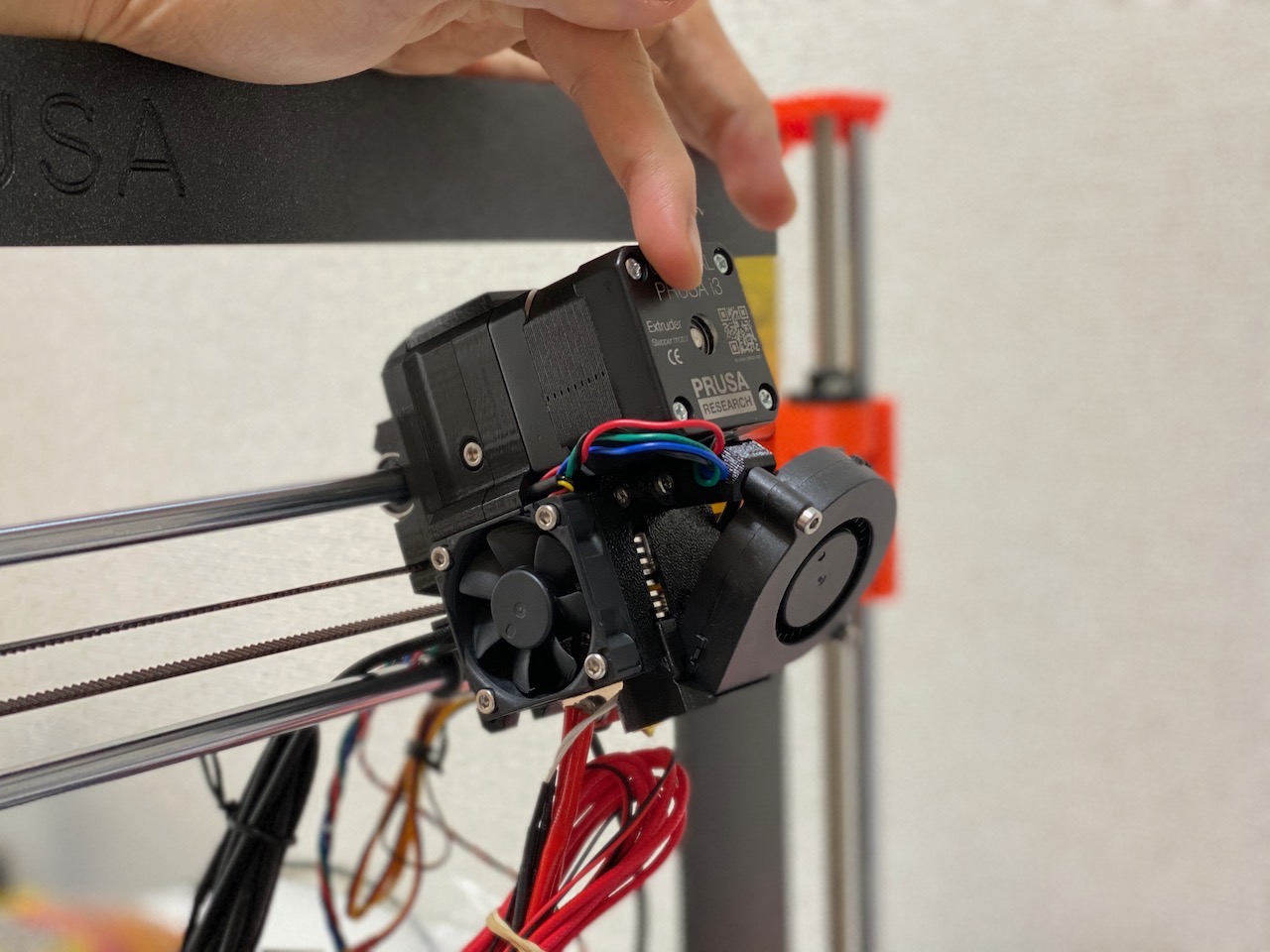
ここまでやって、こんな感じ。
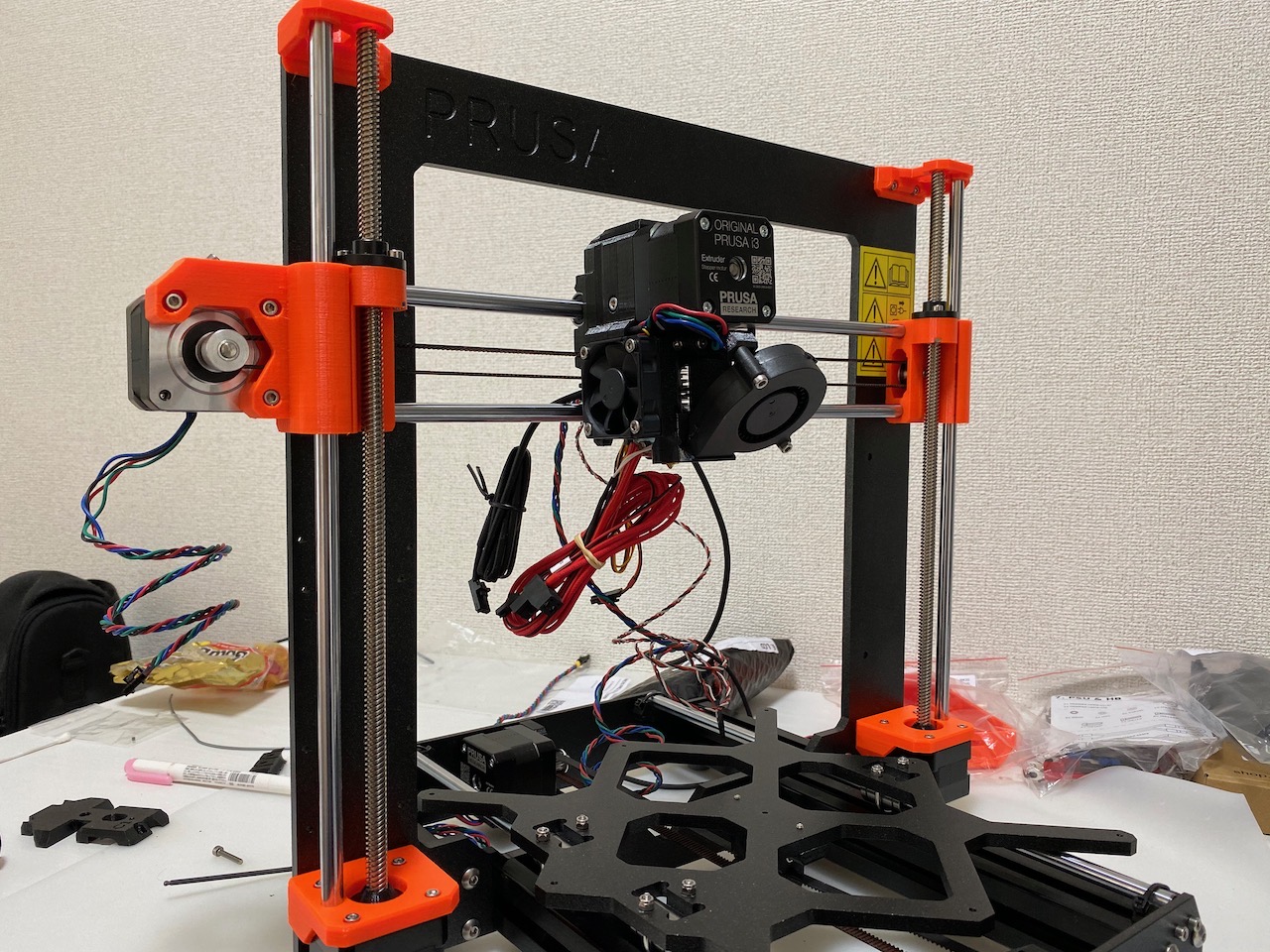
さらに、操作パネルを取り付けたり、電源ユニット (PSU) を取り付けたり、ヒートベッドを取り付けたりする。このへんは楽勝。
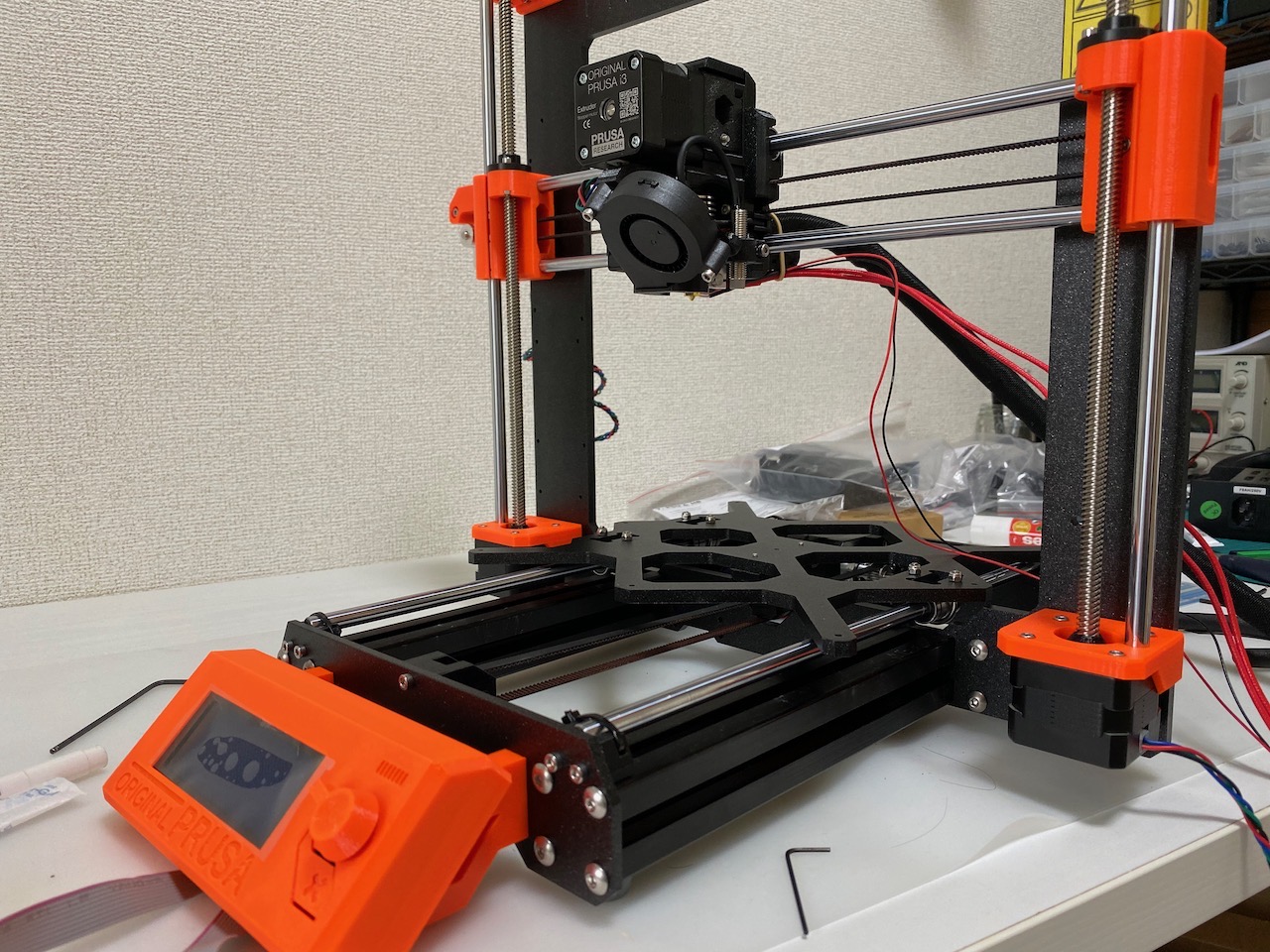
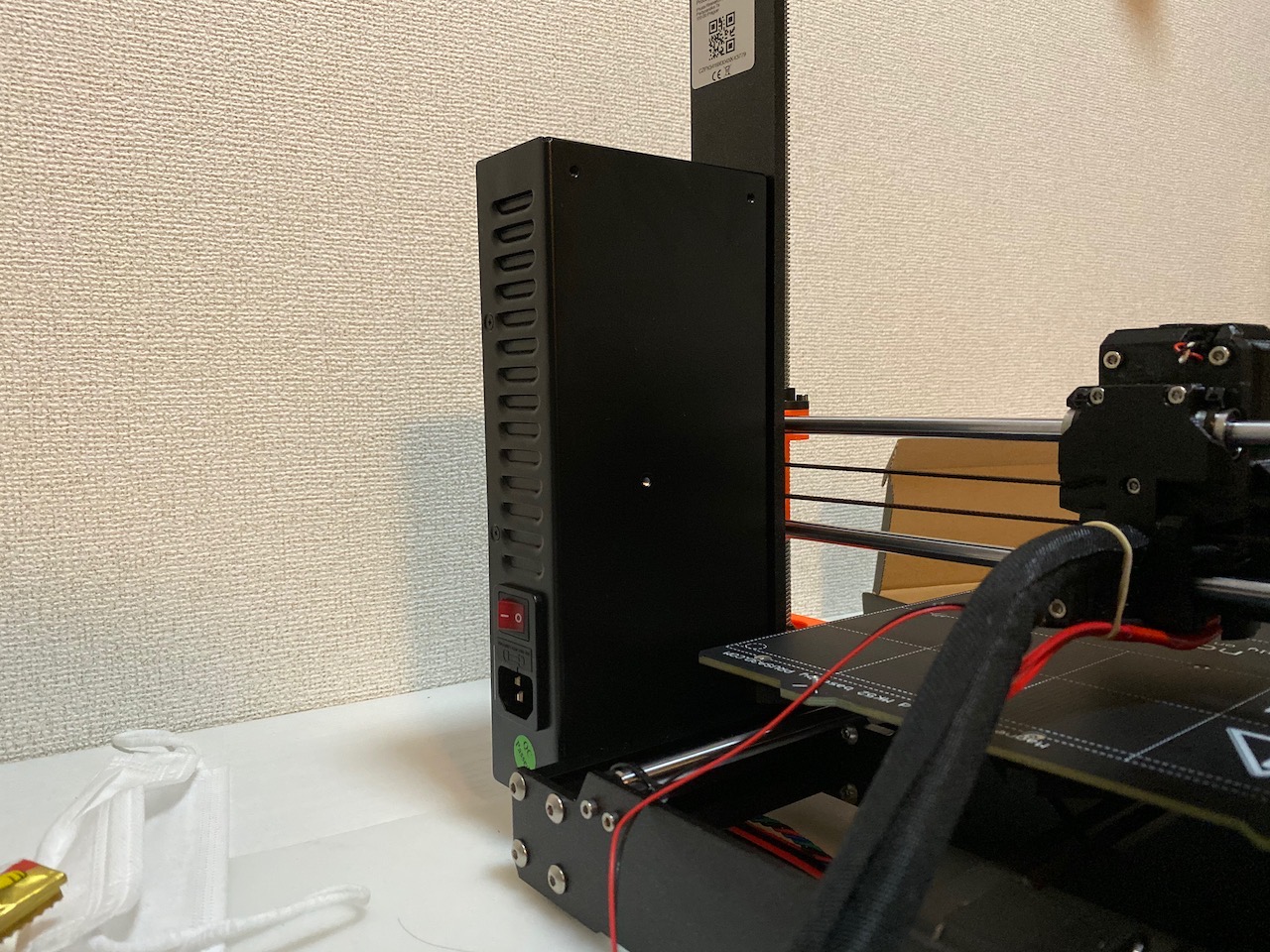
最後に、マザーボードを取り付けて配線する。ボックスが狭くてやりにくい。ケーブルの処理はけっこう厄介。
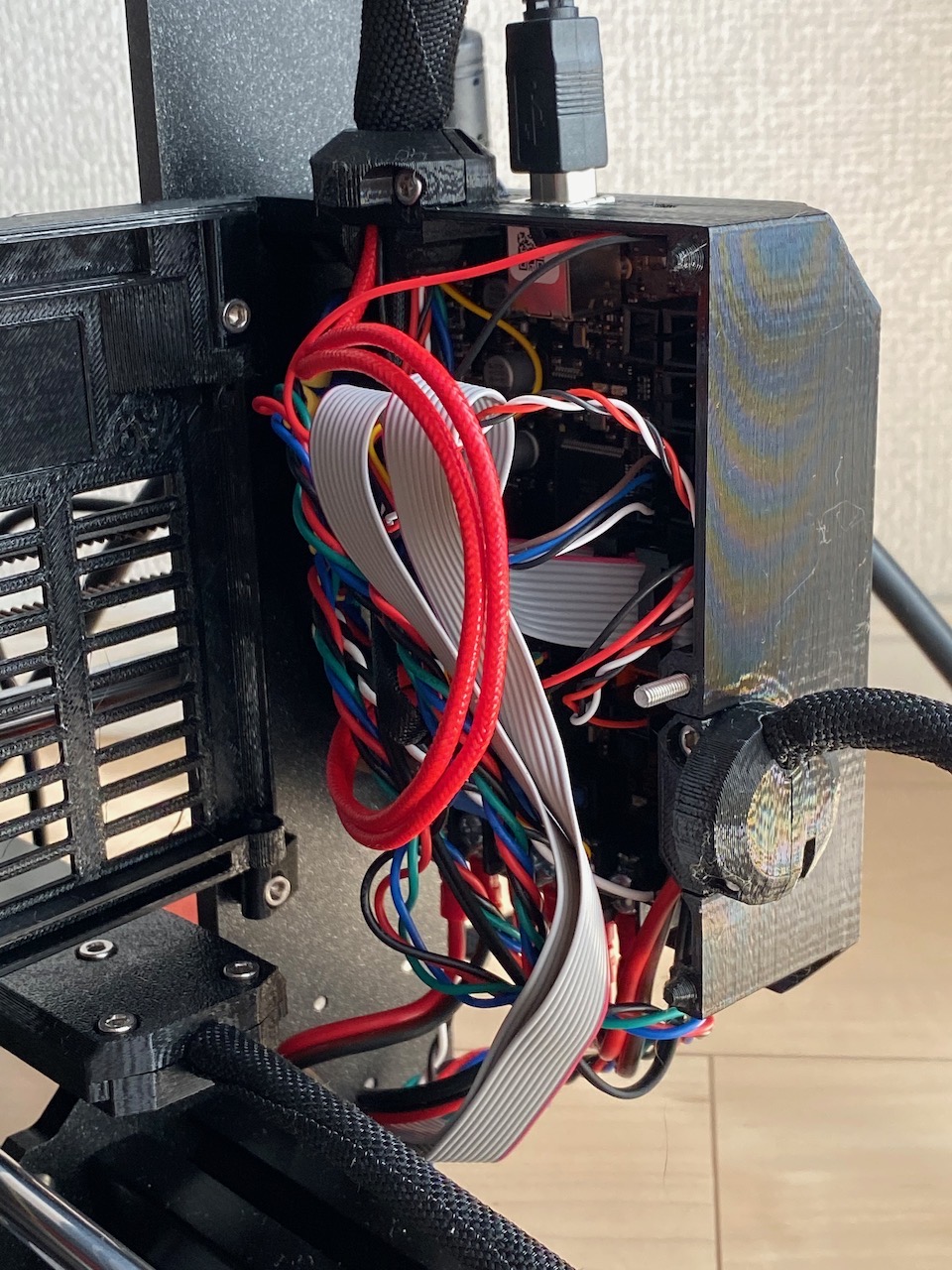
これでおわり。完成。
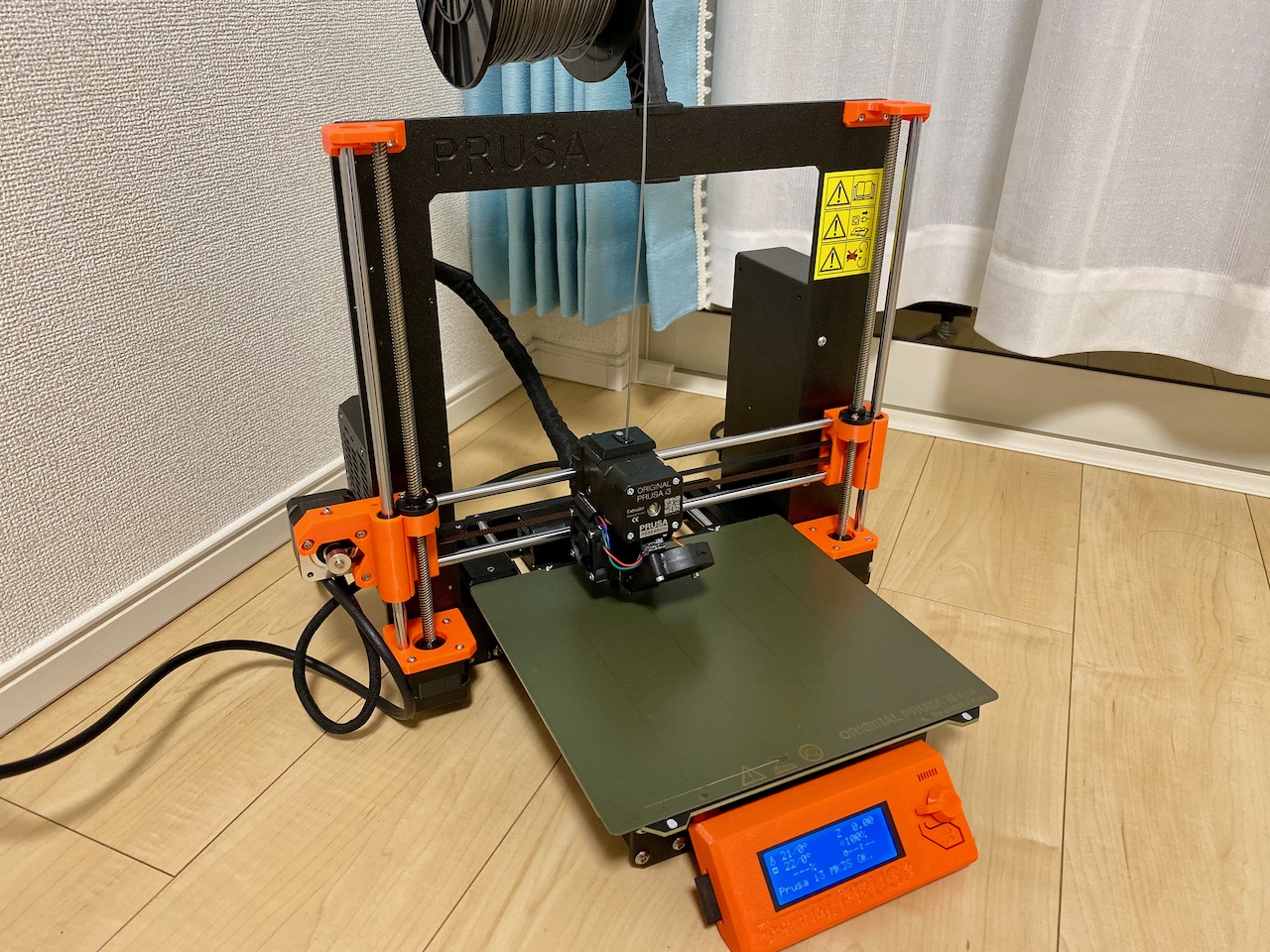
キャリブレーション
初回起動時はセルフテストが行われる。電気的な部品(ステッピングモータ、ファン、ヒーター、センサー、etc.)の動作をそれぞれチェックしてくれる。こういうチェックがあるのは良い。
その次はキャリブレーションを行う。エクストルーダにPINDAセンサーというのがついていて、そのセンサーで印刷台(ヒートベッド)の上をあちこちスキャンして、X, Y, Z軸のゆがみや、印刷台 (heatbed) のゆがみを測定する。この結果を、印刷時のソフトウェア補正に利用するらしい。
キャリブレーションはほぼ全自動で進む。
巷の評価によると、このキャリブレーションがよくできているのがPrusa i3の強みだそうだ。つまり、筐体だけでは出せない精度を、優秀なセンサーと優秀なソフトウェアで実現するということらしい。
キャリブレーションの途中で、ヒートベッドの上にスチールシートを取り付ける。(ちなみに実際に印刷するときは、このスチールシート上で印刷する。)
スチールシートの上で、さらにキャリブレーションを進めていく。
キャリブレーションが終わると「X軸とY軸は垂直です。おめでとう」という英語の表示が出た。どうやら最良の結果らしくて安心した(しかも詳細情報によるとskew 0.00°)。ちなみにネットの情報によると、「わずかに歪んでいるが問題ないよ。グッジョブ」という表示が出ることもあるらしい(特に旧バージョンのMK2で)。仮にそういう結果になっても、ソフトウェアが優秀なので出力品質にほぼ影響しないらしい。
テスト印刷
印刷は、SDカードにデータを入れて行うか、PCと接続して行う。SDカードから印刷するならPCを接続する必要はない。
印刷用データは、CNC工作機械の制御で標準的に使われている “gcode” という形式を使う(このデータを自分で作るときは、3DCADや3DCGソフトで作った3Dモデルを、「スライサー」と呼ばれるソフトウェアで処理する)。
付属のSDカードに入っていた「Treefrog 50μm」(アマガエルみたいなモデル)を印刷してみることにした。50μm (=0.05mm) というのは積層レイヤ1枚の厚みを表している。50μmは熱溶解積層法のプリンタにとってはけっこう精密なデータらしい。他のサンプルデータは150μmや200μmが多い。
液晶画面の指示の通りにフィラメントをエクストルーダに挿入する。フィラメントを挿入すると、フィラメントセンサーが働いて、自動で巻き込みが始まる。
印刷するTreefrogのサイズはけっこう小さいが、精密なデータなので印刷に4時間弱かかるという表示が出た。
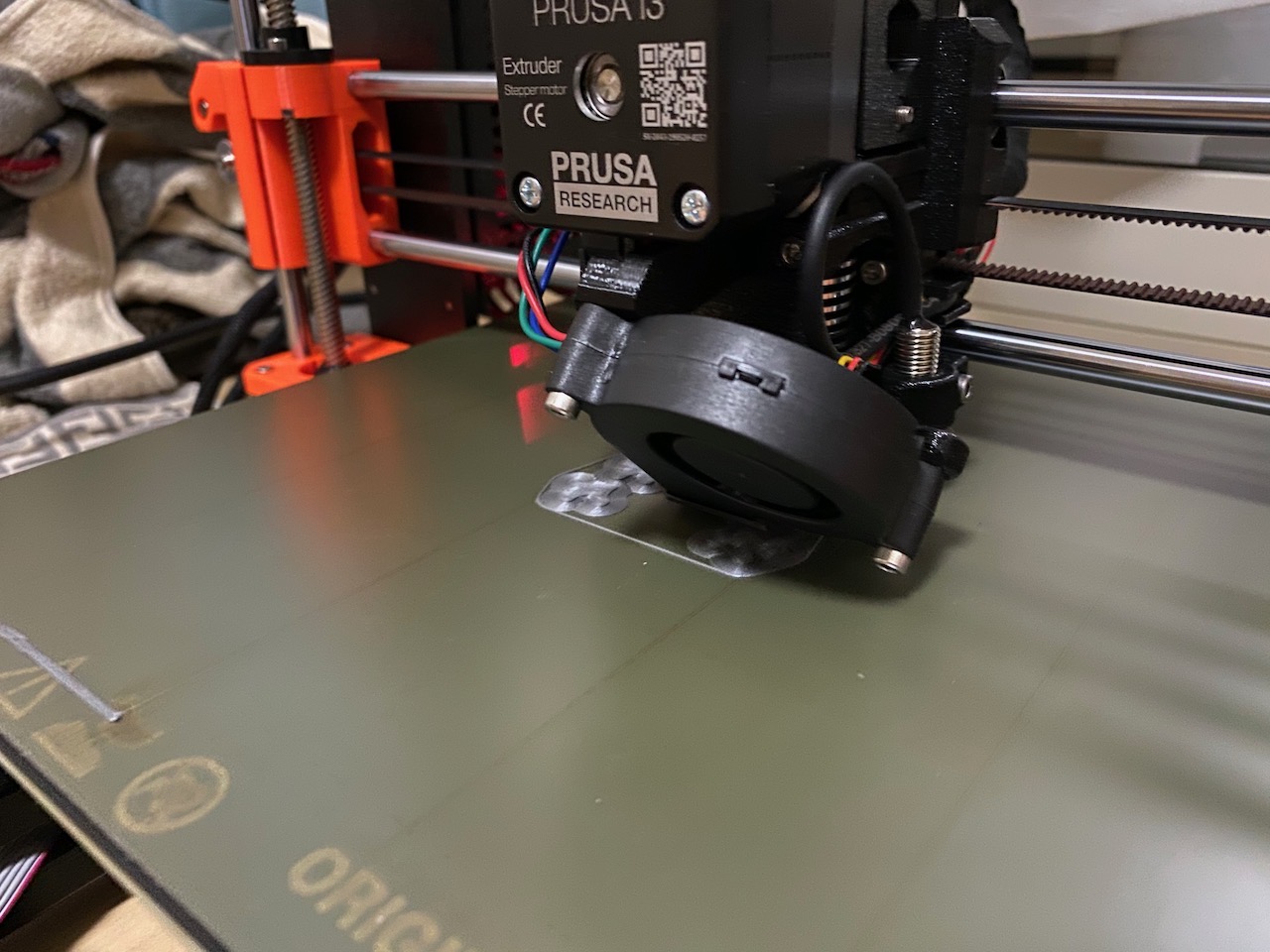
印刷をスタートさせて、すごく疲れていたので昼寝した。で、目が覚めたら何のエラーもなく出来上がっていたので拍子抜け。
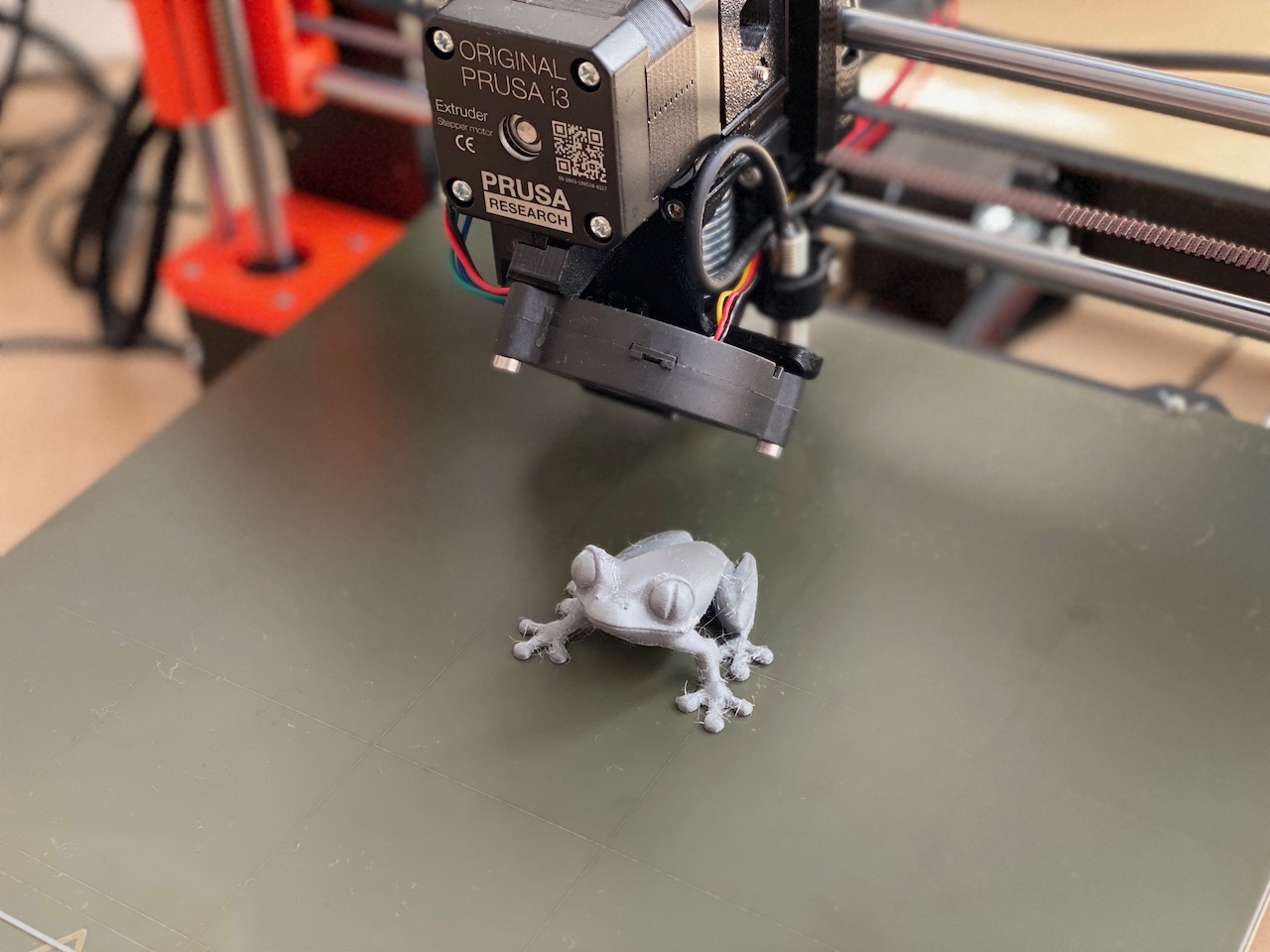
スチールシートをプラットフォームから取り外して、シートをグニャリと曲げると印刷物(カエル)がシートから剥がれる。
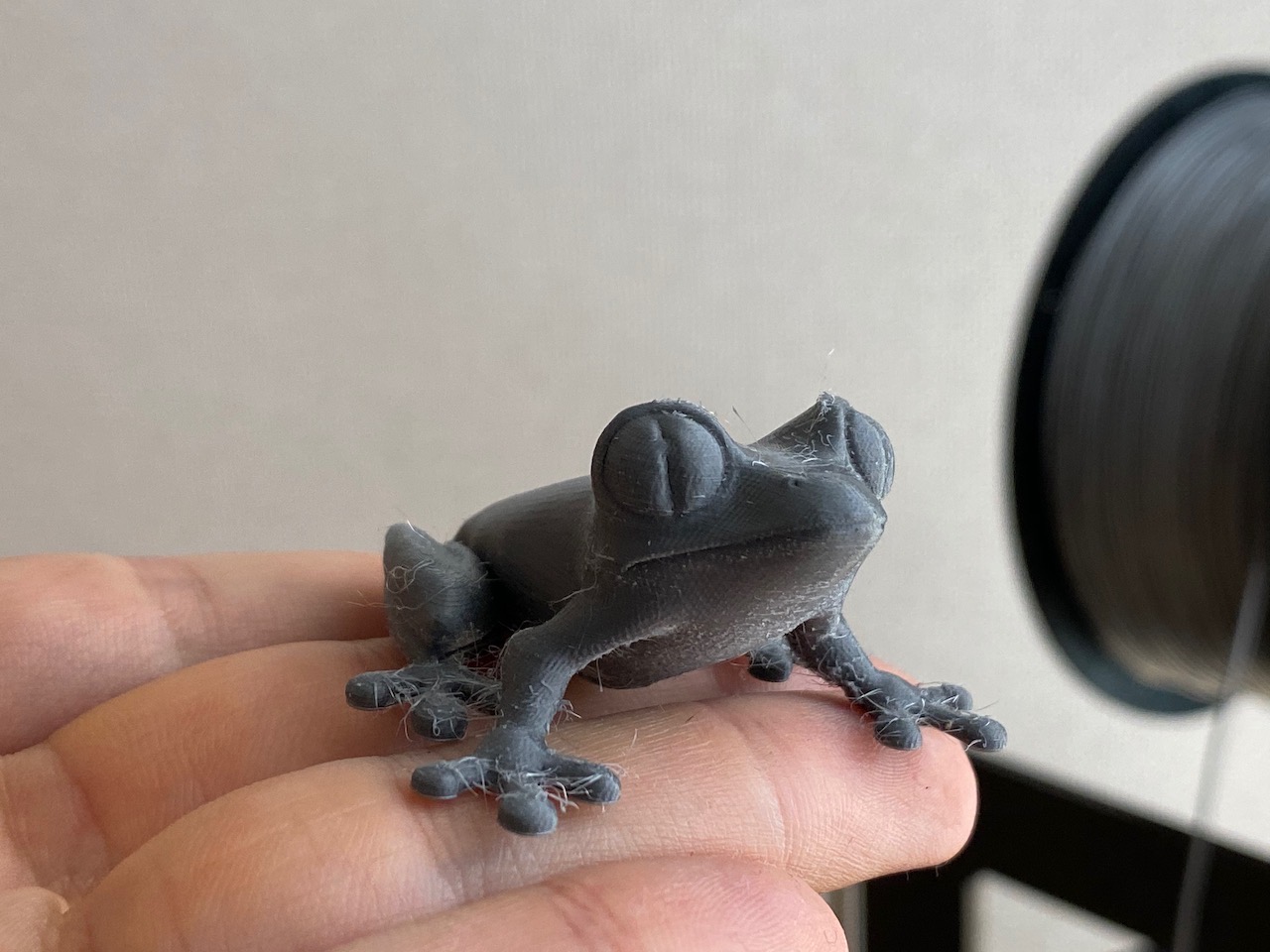
背中はつるつる。
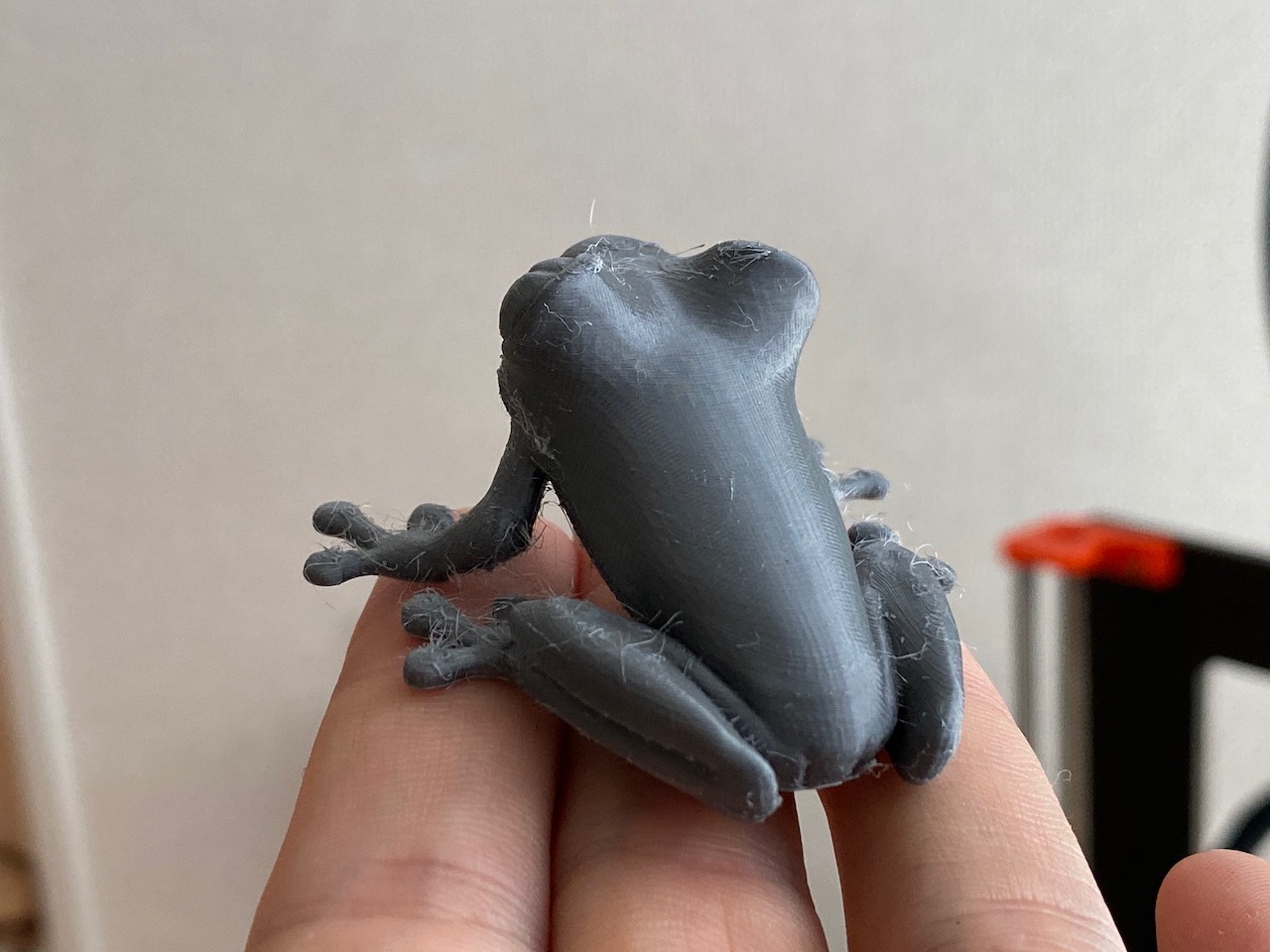
蜘蛛の糸のようなものが生じていて汚いが、複雑なモデルにおいてこれが発生するのはある程度仕方がないようだ(Stringingという)。人間の手で研磨などの処理をしてやれば綺麗に仕上がる。
わかったこと
- 熱溶解積層法の3Dプリンタはあくまでホビー用…と思いきや、このプリンタの部品が3Dプリントで作られているように、実用可能な製品のパーツを作ることもできる。
- 動作音は想像していたよりも静かだった。置く場所や方法を工夫すれば深夜のアパートでも余裕で動作させられると思う。より静音にするためのステルスモードもあるらしいが、まだ試していない。
- 組み立て作業に高い精度は求められない。常識的な丁寧さで作ればちゃんと動く。
- ハードウェア自体はけっこう単純なので、それを支援するソフトウェアが重要な役割を果たす。
- 機械系の人たちには常識なんだろうけど、ステッピングモータとベルトだけでこういう精度が出せるのはすごい。
- PCをつなぎっぱなしにする必要はない。SDカードで印刷できる。良い。
- フィラメントを押し出す部分をエクストルーダ (extrude = 押し出す) と呼ぶ。ステッピングモータは、XYZの各軸に加えて、エクストルーダにも付いている (E軸)。これによって、フィラメントをヒータ内に取り込む量、つまり射出量が制御される。
- エクストルーダにはフィラメントを溶かすためのヒーターが付いていて、稼働時は200〜250℃になる。物体を出力するプラットフォームにも造形物が外れないようにするためのヒーターがついていて、こちらは60〜80℃くらいになる。これらの温度はフィラメントの材質 (PLA, ABS, PETG, etc.) に応じて適切に変える。
今後
自分はこういうカエルを印刷したいわけではない。
いずれにしても、3DCAD/CAM/CAEを覚えて損はないだろう。Fusion 360を少しだけ触ってみたが、目的の形状を作る作業はパズルを解くみたいで楽しい。単に図面を引くだけでなく、画面上で構造物を組み立てて稼働させたりできるのもすごい。まだぜんぜん分かってない。
リニアベアリングの品質
組み立て時に、リニアベアリングが金属ロッド上で結構ひっかかる感じがした。実際に動作させるまでずっとこれが気がかりで、気になってしまって組み立て作業が止まったりした。
結果的には出力品質に問題はなさそうなので、ベアリングの品質が多少悪くても深刻な影響はないのかもしれない。ただし静音性に影響している感じはしなくもない。印刷時には各軸が高速に移動することがたまにあるが、そのときはけっこうギャーギャー鳴く。
フォーラムの情報を見ると、日本のMISUMI製などの上質なベアリングとロッドに交換する人もいるようだ。